There are few things in the automotive world more exciting than the arrival of a critical part. It’s the final piece of a puzzle for a restoration, the high-performance upgrade for a weekend at the track, or the essential component that gets a customer’s daily driver back on the road. The journey this part takes, from the seller’s shelf to the buyer’s garage, is the final, crucial step to project success. But while it may seem as simple as putting an item in a box and handing it to a courier, the reality is far more complex.
The path from Point A to Point B is paved with hidden pitfalls, and a single, seemingly minor mistake when shipping automotive parts can quickly spiral into thousands of dollars in damage, weeks of project-halting delays, and a severely damaged professional reputation.
This comprehensive guide is designed to arm you with the knowledge to navigate these potential disasters. We are going to move beyond basic advice and delve into the 10 most common-—and costly-—mistakes we see professionals and enthusiasts make every single day. By understanding these errors and learning how to prevent them, you can implement a professional-grade shipping strategy. This ensures your valuable automotive components arrive exactly as they left your hands: safe, sound, and ready for installation.
Mistake #1: Using Inadequate or Improper Packaging
This is, without question, the single most common and catastrophic point of failure in the shipping process. The packaging is your part’s first, last, and only line of defense against the harsh realities of modern logistics—automated sorting belts, bumpy roads, and countless transfers between trucks and depots. Treating it as an afterthought is a recipe for disaster.
The “One-Size-Fits-All” Fallacy
A common error is grabbing any available box and assuming it’s good enough. For heavy, dense, or irregularly shaped automotive parts, a standard single-wall cardboard box from a local store is simply not sufficient. These boxes lack the structural integrity to prevent puncture or collapse under the weight of other packages.
- The Proactive Solution: Always opt for heavy-duty, double-wall (or even triple-wall for extremely heavy items) corrugated boxes. The added rigidity and strength are well worth the minimal extra cost and provide a far more robust shell to protect your valuable components.
Choosing the Wrong Cushioning Material
The goal inside the box is to achieve zero movement. If the part can shift, it can be damaged. Many people reach for newspaper or a handful of packing peanuts, but these are terrible choices for most automotive parts. Heavy metal components will compress newspaper into uselessness, and small, dense parts will simply sink to the bottom of a box full of peanuts, leaving them vulnerable against the box wall.
- The Proactive Solution: Invest in high-quality cushioning materials. High-density foam sheets, custom-cut foam inserts, spray-in foam that creates a custom cradle, and large-bubble wrap are far superior. As a rule of thumb, there should be at least two to three inches of dense cushioning material between your part and every wall of the box.
Forgetting the Double-Box Method
For extremely fragile or high-value items—such as headlight assemblies, delicate electronic sensors, infotainment screens, or classic car chrome trim—the double-box method is the professional standard.
- The Proactive Solution: First, wrap the part securely and place it in a well-cushioned inner box. Then, place that entire box inside a second, larger heavy-duty box, with at least two inches of cushioning material (like foam sheets or spray foam) between the inner and outer boxes. This creates a “suspension” system that absorbs shocks and vibrations before they can reach your component.
Failing to Seal Securely
The world’s best box is useless if it’s held together by flimsy tape. Using cheap masking tape, cellophane tape, or a single strip of low-quality packing tape is asking for the box to burst open in transit.
- The Proactive Solution: Use a high-quality, pressure-sensitive plastic packing tape that is at least two inches wide. Apply tape generously using the “H-tape” method: tape down the center seam where the box flaps meet, and then tape along the two edge seams. This creates a secure seal that reinforces the box’s structure.
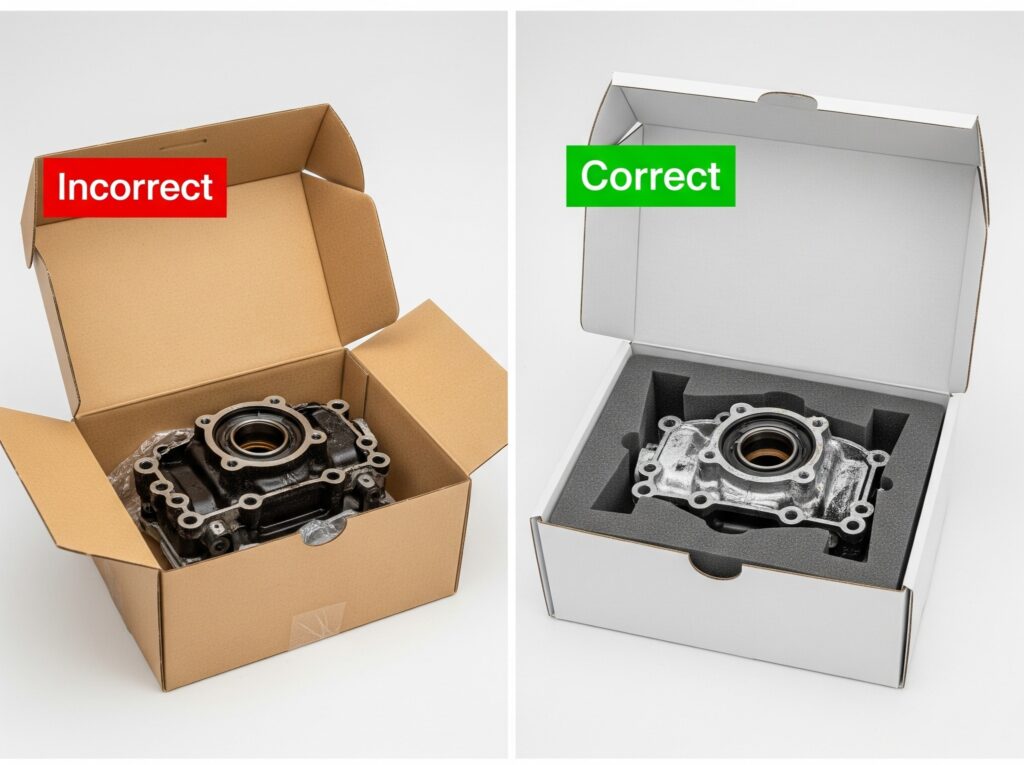
Mistake #2: Not Preparing the Part Itself for Shipment
What you do before the component even touches the box is just as crucial as the packaging itself. Automotive parts are often greasy, have moving elements, or contain residual fluids, all of which must be addressed.
Failing to Completely Drain Fluids
This is a cardinal sin in the world of shipping and can have serious consequences. Engines, transmissions, differentials, power steering pumps, and hydraulic components can all contain residual fluids. If these leak during transit, they can saturate and destroy the cardboard packaging, create a hazardous material situation, void your shipping agreement with the carrier, and potentially damage other items in the same shipment.
- The Proactive Solution: Drain all fluids completely. Take the extra time to tilt the component on all axes to ensure every last drop is removed. Then, securely plug all fluid inlets and outlets. Place the part in a heavy-duty plastic bag or wrap it in industrial plastic sheeting as a final layer of protection against any unforeseen drips.
Leaving Components Loose or Exposed
Many automotive parts have smaller, fragile elements attached to a larger, more robust body. Think of the delicate plastic sensors on an engine block, the connectors on a wiring harness, or the mounting tabs on a headlight. Leaving these exposed is asking for them to be snapped off.
- The Proactive Solution: Individually protect these fragile appendages before wrapping the main component. Use small bubble wrap and tape to secure sensors, connectors, and other breakable pieces against the main body of the part. This prevents them from snagging or being damaged by shock.
Not Cleaning the Part
While it may seem purely aesthetic, shipping a dirty, greasy part poses practical risks. Packing tape and labels will not adhere properly to an oily or grimy surface, compromising the security of your packaging. Furthermore, a clean part is easier to inspect for pre-existing damage, which is crucial for documentation (see Mistake #8).
- The Proactive Solution: Degrease and clean the component thoroughly before you begin the packaging process. A clean, dry surface ensures a much more secure and professional packaging job from start to finish.
Mistake #3: Treating All Automotive Parts the Same
A fender is not an ECU, and an axle is not a chrome grille. Each category of automotive component has unique vulnerabilities and requires a specialized packaging and shipping strategy. A one-size-fits-all approach is a common mistake that leads to predictable types of damage.
Shipping Large Body Panels (Hoods, Doors, Fenders)
These items are the definition of “awkward.” They are large, relatively lightweight for their size, and extremely susceptible to dents, dings, and scratches. Placing them in a simple cardboard box, even a large one, is almost guaranteed to result in damage as other heavy items are inevitably stacked on top of or against them in a truck.
- The Proactive Solution: These parts almost always require LTL (Less-Than-Truckload) freight shipping rather than a standard parcel service. The best practice is to build or use a custom wooden crate. If a crate isn’t feasible, the panel should be wrapped in multiple layers of foam or blankets and strapped securely to a pallet to prevent it from being treated like a regular box.
Shipping Heavy & Dense Items (Engines, Axles, Transmissions)
For these components, the primary risk is their own immense weight and the potential for them to break through inadequate packaging. A 700lb engine block that breaks loose from its pallet is a literal wrecking ball inside a transport trailer, capable of destroying itself and everything around it.
- The Proactive Solution: These items MUST be shipped via freight on a robust pallet or in a sturdy crate. The component must be securely fastened to the pallet using high-tensile metal or plastic strapping. Simply placing it on the pallet and shrink-wrapping it is not enough. The goal is to make the part and the pallet a single, immovable unit.
Shipping Wheels and Tires
A common mistake here is simply slapping a label on the tire tread or shipping an expensive alloy wheel in a single, flimsy box. The tire can be damaged by sorting equipment, and the beautiful face of the wheel is highly susceptible to scratches.
- The Proactive Solution: For wheels, always place a thick, rigid piece of cardboard over the face of the wheel before placing it in a heavy-duty, double-wall box. For tires, it’s best practice to wrap them in pairs and apply protective cardboard discs to the wheel faces if they are mounted.
Shipping Delicate Electronics (ECUs, Clusters, Infotainment)
With these parts, the risk isn’t just physical shock; it’s electrostatic discharge (ESD), which can fry the sensitive internal circuitry without leaving a single external mark.
- The Proactive Solution: These components must first be placed in an anti-static bag (often pink or silver). Only then should they be wrapped in bubble wrap and double-boxed to protect against physical damage.
Mistake #4: Incorrect or Incomplete Labeling
A perfectly packaged part is worthless if the carrier doesn’t know where to send it. Labeling errors are a frustratingly simple but common cause of delays and lost packages.
The Perils of Reused Boxes
Saving money by reusing a box is smart, but failing to prepare it properly is a critical error. Automated sorting machines used by all major carriers scan for barcodes and addresses. If your box has multiple old labels and barcodes on it, the machine can easily get confused, sending your package to the wrong city or into a loop of endless re-sorting.
- The Proactive Solution: Before using an old box, take an extra minute to completely remove or totally black out every single old shipping label, barcode, address, and tracking number with a permanent marker.
The “Duplicate Label Inside” Pro Trick
Shipping labels are surprisingly fragile. They can be torn, scuffed, or damaged by rain, rendering them unreadable. If this happens, your package can end up in a carrier’s overgoods or lost-and-found warehouse with no way of identifying its origin or destination.
- The Proactive Solution: Always print a second, identical copy of your shipping label and place it directly on top of the part inside the box before you seal it. If the exterior label is ever destroyed, the carrier can open the package and still find the critical information needed to complete the delivery.
Using Handling and Orientation Labels
While you can’t assume every handler will treat your package like their own, using clear visual cues can only help.
- The Proactive Solution: Apply brightly colored “Fragile,” “Heavy,” or “This Way Up” stickers to the outside of your package. For items that must remain in a specific orientation (like an engine on a pallet), directional arrows are essential.
Mistake #5: Ignoring International Customs Documentation
For those shipping automotive parts across borders, this mistake can turn a simple shipment into a bureaucratic nightmare. Customs agencies are meticulous, and any error or omission can halt your shipment for weeks.
The Vague Commercial Invoice
A commercial invoice is a legal document required for all international shipments. A common mistake is using vague descriptions like “Used Car Parts” or “Auto Components.” This is a major red flag for customs officials and will almost certainly trigger a manual inspection and delay.
- The Proactive Solution: Be incredibly specific. Your commercial invoice must list each individual item in the shipment, its quantity, its country of origin, and its value. For example, instead of “Car Parts,” write “1 x 2018 Honda Civic Water Pump (Made in Japan), 2 x Bosch Front Brake Pads (Made in Germany).”
Getting the HS Code Wrong
The Harmonized System (HS) code is a standardized international code used to classify traded products. Every item has a specific code, and this code is used to determine the duties and taxes owed. Guessing or using an incorrect code is a frequent error.
- The Proactive Solution: Use online government resources or your carrier’s tools to find the correct HS code for each part you are shipping. Accuracy here is critical for smooth clearance.
Declaring an Unrealistic Value
It can be tempting to undervalue a shipment on the commercial invoice to try and save the recipient money on duties and taxes. This is illegal and a terrible idea. Customs officials are experts in valuing goods and use databases to check for discrepancies. If caught, your shipment can be seized, and both you and your customer can face significant fines.
- The Proactive Solution: Always declare the true and accurate transaction value of the goods. Honesty and accuracy are the fastest way through customs.
➡️ External Link: For shipments to or from Canada, review the Canada Border Services Agency’s Step-by-Step Guide to Importing for detailed requirements.
Mistake #6: Misunderstanding Declared Value vs. Insurance
This is arguably the most financially dangerous mistake on the entire list. It stems from a fundamental misunderstanding of what carriers offer and where their responsibility ends.
What “Declared Value” Really Is
When a carrier’s shipping software asks you to “Declare a Value,” it is very easy to assume you are purchasing insurance. You are not. You are simply paying the carrier a higher fee to increase their maximum limit of liability. All the other terms still apply: you still have to prove the carrier was negligent, the claims process is still difficult, and many types of damage are still not covered. It is often an expensive way to buy slightly better, but still inadequate, protection.
The Sobering Reality of Carrier Liability
As mentioned, the default liability for most carriers is shockingly low, often just $2 per pound. This means that if you don’t pay extra for a higher declared value, that is the absolute most you can ever hope to recover, and only if you can prove their negligence. Let’s use a single, powerful example:
- An aluminum cylinder head for a performance car weighs 20 lbs but is worth $1,500. If it is dropped and cracked, the carrier’s maximum liability is just $40. You are out $1,460.
The Knowledge Gap
Relying on this minimal liability-—or even the carrier’s inflated “declared value” option-—is the number one reason that businesses suffer massive, preventable financial losses from shipping incidents. Understanding this critical gap between a carrier’s liability and true, comprehensive third-party insurance is the first and most important step toward building a truly professional and secure shipping strategy.
Mistake #7: Failing to Document Everything with Photos
In the event of a dispute or a damage claim, the party with the best documentation almost always wins. Failing to create a photographic record of your shipment is throwing away your most powerful evidence.
- The Proactive Solution: Implement a simple, three-step photo process for every valuable shipment:
- Before: Take clear, well-lit photos of the part from all angles before it is packaged. Document its pre-shipment condition and be sure to capture any existing serial numbers.
- During: Take photos as you are packaging the item. Show the layers of cushioning, the quality of the materials, and how securely the part is nestled in its box or crate.
- After: Take photos of the final, sealed package from all sides, including a clear shot of the shipping label.
This small-time investment creates an indisputable record that can be invaluable if you ever need to file a damage claim.
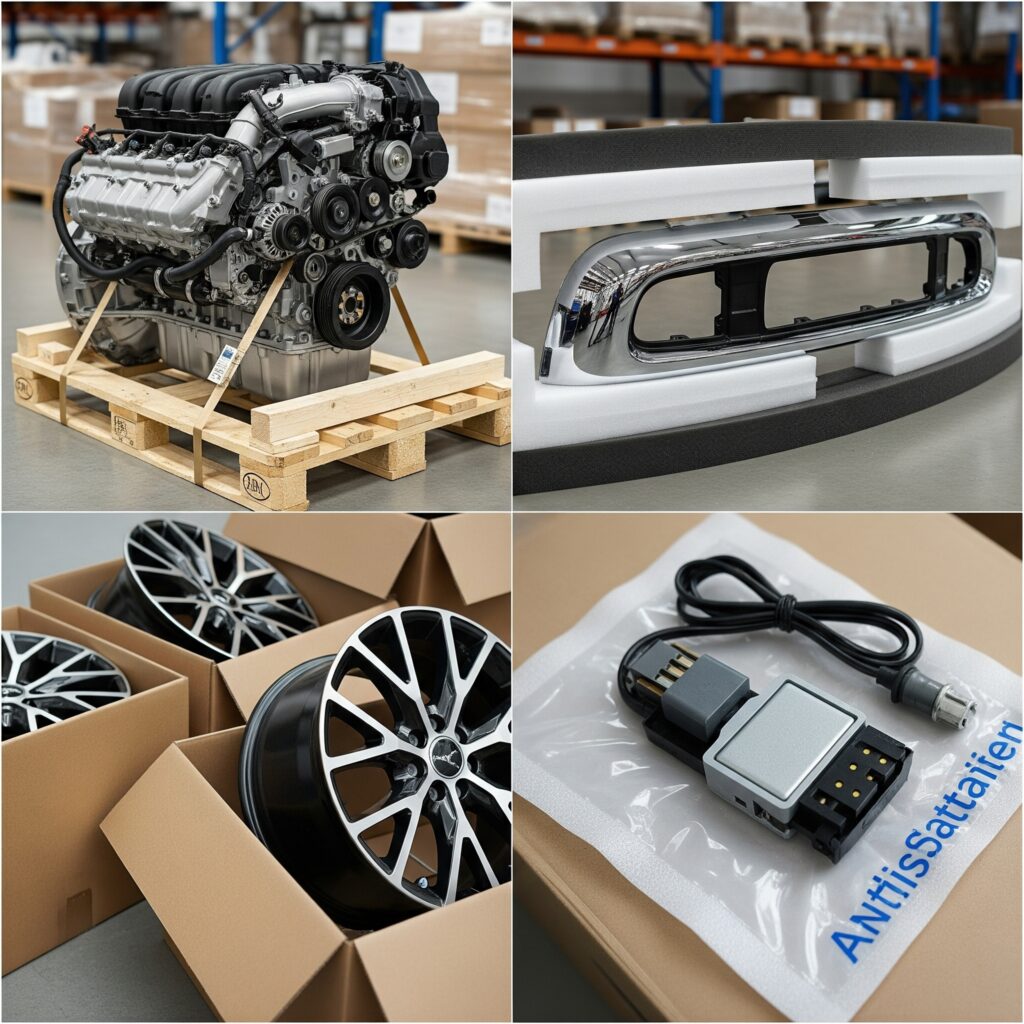
Mistake #8: Not Preparing the Recipient for Delivery
The shipping process doesn’t end when the truck leaves your dock; it ends when the recipient safely accepts the package. Failing to communicate best practices to your customer is a mistake that can jeopardize an otherwise perfect shipment at the final hurdle.
- The Proactive Solution: Send a brief communication to your customer before the package arrives. Instruct them to thoroughly inspect the exterior of the box or crate for any signs of major damage-—crushed corners, punctures, tears, or signs of leaking-—before they sign the delivery receipt. If significant damage is visible, they should either refuse the shipment or make a detailed note of the damage on the delivery receipt before signing. In some legal jurisdictions, signing for a package without noting damage can be interpreted as “accepted in good condition,” which can make a future damage claim more difficult.
Mistake #9: Forgetting about Hazardous Materials
While most auto parts are harmless, some can be classified as hazardous materials (Hazmat) and require special handling and declaration. Ignoring this is a serious compliance error.
- The Proactive Solution: Be aware of common automotive hazmat items, which can include:
- Airbags (contain explosive charges)
- Batteries (especially lithium-ion batteries)
- Certain paints, solvents, and pressurized aerosols.
- Seatbelt pretensioners.
If you are shipping automotive parts that fall into these categories, you cannot use standard shipping services. You must use a carrier certified to handle dangerous goods and follow all regulations for declaration, labeling (with proper hazmat placards), and packaging.
Mistake #10: Believing “It Won’t Happen to Me”
The final and most pervasive mistake is one of mindset: complacency. It’s easy to ship dozens or even hundreds of packages without an issue and begin to believe that damage or loss is a rare event that only happens to other people.
- The Proactive Solution: Acknowledge the statistics. Industry reports consistently show that a small but significant percentage of all packages are damaged or lost in transit. While the overall rate may be low, for a business shipping valuable goods, the financial impact of that one “rare” event can be devastating. A professional approach means treating every single shipment as if it’s the most important one you will ever send. Hope is not a strategy; preparation, diligence, and a robust protection plan are what separate successful businesses from those who eventually suffer a major, preventable loss.
Conclusion: From Shipper to Logistics Professional
Successfully shipping automotive parts is about much more than just logistics; it’s about mastering the details. From the quality of your packing tape and the specificity of your customs invoice to the way you prepare your customer for delivery, every step in the process matters. By consciously understanding and avoiding these 10 common and costly mistakes, you elevate your process from that of a casual shipper to a true logistics professional. You actively protect your valuable assets, your hard-earned reputation, and your company’s bottom line.
Now that you have a firm grasp of the common pitfalls and, most importantly, the critical financial gap left by standard carrier protection, you may be wondering what a better, more secure protection strategy looks like. The next step is to explore the dedicated solutions designed to fill that gap.
➡️ Read our follow-up guide: “A Head-to-Head Comparison of Automotive Shipping Insurance Options” and take the next step toward a more secure shipping process.
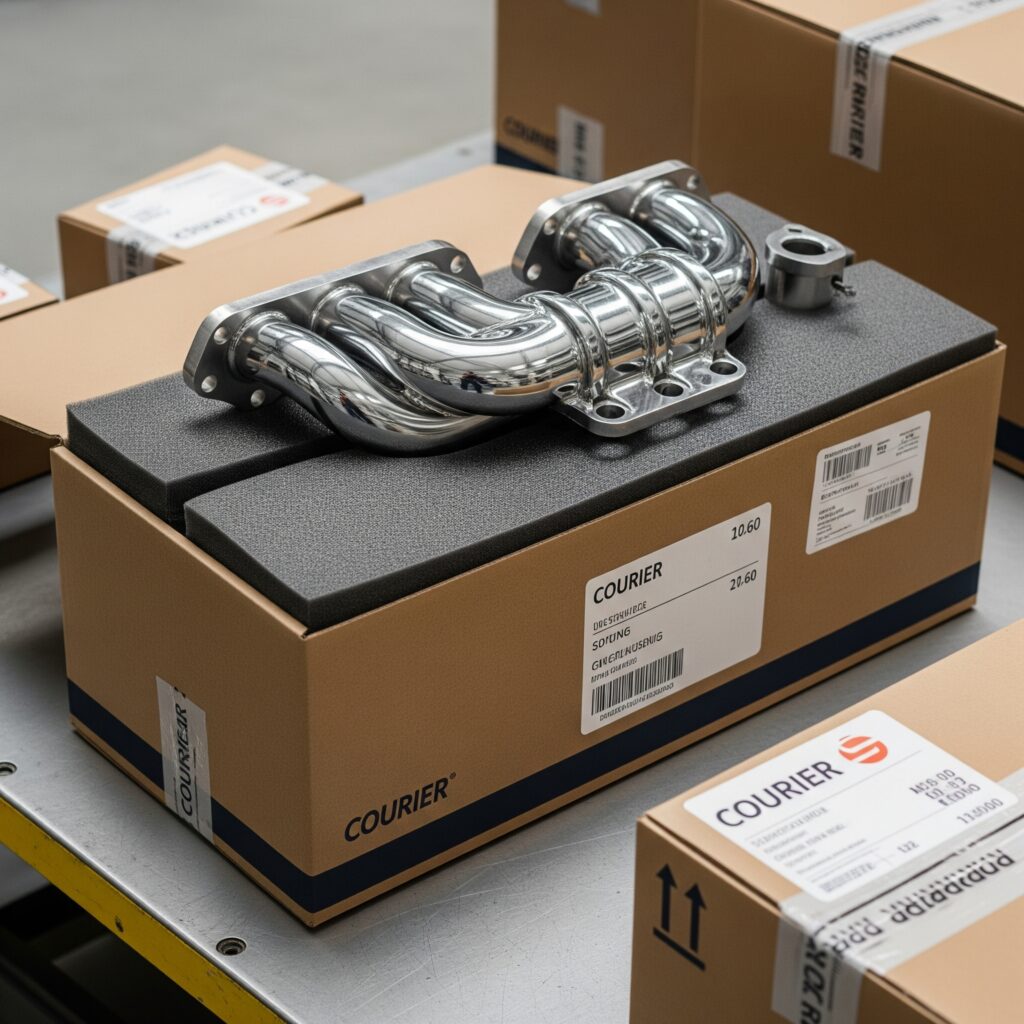
Additional Resources
- Shipping Insurance Overview
- Automotive Industry Page
- Get a Quote
- How to Package Automotive Parts for Safe Shipping
- Shipping Insurance FAQs
- Freight Insurance for Aerospace & Aviation
- Automotive Logistics – Supply Chain Management
- Transport Canada – Motor Vehicle Safety
- Auto Care Association
- SEMA (Specialty Equipment Market Association)
- Red Stag Fulfillment – How to Ship Car Parts